Well here's an interesting discovery I would like to share. Some of the gurus might know this, but I haven't read anything on the Samba about it. I've found a way to run a 12 volt starter on a 6 volt flywheel with very little work involved.
This is an alternative to replacing the flywheel (& clearancing the bellhousing) or running a 6 volt starter in a 12 volt conversion. This could also be an alternative for running a 6 volt starter on a 12 volt flywheel (though I don't know if/why someone would need to).
So here's the rundown. I found that the bushing inside the 12v starter gear perfectly fits into the bushing in the 6v starter gear. This allows you to put the larger diameter 6v gear onto the 12v armature axle. why? so that you won't need to change flywheels to change starters, after a 12v conversion.
Now the only reason I even did this is that my 6v starter took a crap, and I had bought a new rebuilt 12v starter that I was going to cannibalize. Otherwise, the 6v starter does really well all juiced up on 12 volts, though it may help to replace the 6v solenoid with a 12v.
First things first. Unless you have more than one 12v starter lying around, you'll need to buy yourself one of those bushings for the 12v starter that fit in the bellhousing. do this before you go tearing into your starter. If you have more than one 12v starter then you're golden. I might even suggest it, so that you don't need to pull out the bushing already in there, which would be difficult with the engine still in the car.
so here's the new rebuilt 12v starter that I got for a killer 55 bones.
First thing you'll need to do is begin disassembling the 6v starter. I don't think you need to take off the solenoid but it may make things easier.

The screws on these things are old! so use the correct screwdriver, or you'll strip it and have to drill it out like I did! Same with the other screws.
Unscrew the top nipple cover, and take out the retaining clip and washers. Then unscrew the two larger screws to take off the end cap. You may need to give the cap a hit with a hammer if it's stubborn.
When you get it of, pull out the brushes that are connected to the case, you can leave the other two on. Then pull of the brush's bracket.

Check out your brushes. If their good, keep 'em around.

Same for the brushes on the case.
Now I read somewhere on the Samba that you can replace these brushes, but they are soldered on, and coated in enamel. I suppose you could replace them, but you'd be harder pressed to find new ones (or some you could make fit) than you would picking up an old starter with decent brushes.
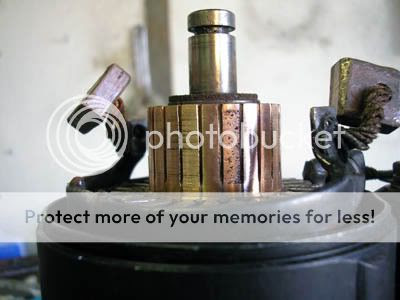
Here is the reason I took on this project. You see the contact point that is all pitted? This picture was taken just after I sanded down the commutator really well, because that contact point, and the one opposite, were severely corroded and I thought the brushes couldn't make contact, leaving me stranded in the parking lots.

This picture was taken the next day, after being stranded again, and clearly there is a short in the armature somewhere, since I had replaced everything except for it.
But back to the project. At this point you should have the cap, bushes, and case all removed, and the armature is still trapped by the top cap/ mounting bracket.

This little bugger had me scratchin' my noggin for a while. But the round piece needs to be tapped down to get the retaining ring off. Then you can slide the gear assembly off the armature axle. (To get the retaining ring back on, slide the round piece on first, then the ring. Use pliers to grip the bottom of the round piece and top of the axle to clip it back over. Start from the side opposite the ring gap.)
Now you have the 6v gear assembly, this is what you're going to put onto the 12v starter.
Go through the same process of disassembling the 12v starter and remove the gear assembly from it also. And if you have another 12v starter do the same thing, it'll be worth it.
Once you have the 12v gear assembly/ies, find a socket or something that closely fits the circumference of the bushing inside the gear and gently tap them out from the inside, there are two of them in there. the rear one may be chipped, both of mine were, it shouldn't be too big of a deal, unless they are both demolished.

Here is the 12v starter bushing being put into the 6v starter bushing. A suspiciously precise fit. I cleaned the inside and out, then added loctite before pressing both in.
If you don't have a second starter, and your bushing are both immaculate, then you might only use one in the gear (though I don't suggest it). The reason you'll need an extra bushing is to put inside the bushing in the bellhouse, which will fit perfectly as well. This will save you the trouble of installing an after-market conversion bushing.

So as you can see here it is a perfect fit. Barely noticeable that one bushing is inside another.

Another consideration I made was that the spiral shaft gears fit together. And of course they did.

Here you can see I pressed an extra bushing into the bushing in the bellhouse. I cleaned and added loctite to this one as well. I add loctite to prevent the bushing from spinning, possibly causing it to come out, or shred to pieces.
Don't forget to re-lube the new bushings!
At this stage you've got your 6v gear assembly with it's new bushings, and so you're just going to re-assemble it onto the 12v starter. Hopefully you remember how it all goes back together. Don't lose the washers/shims that go on the rear of the armature axle, both under the brush bracket and under the nipple cap.
Earlier I was saying that you could possibly use this to put a 6v starter on a 12v flywheel. Well you're just going to remove the bushings from the 12v gear assembly, then put the gear on a 6v starter. It fits perfectly without bushings, but keep it well lubed.

Finally, here is my new rebuilt 12v starter turning over a 6v flywheel. All done without even dropping the engine!
Post Script:
I am interested to know if the after-market bushings might fit inside the gear assembly as well? If not it might be a good new product!
UPDATE (9/2010):
That inner bushing finally disintegrated in my starter sometime this week. It looks like it spun out, maybe I should have used a glue instead of locktite.
Also the inner bushing in the bellhouse is ovaled-out and may go soon too. Both the outer bushings are intact and look unaffected. I'm not sure which one is causing the starter to intermittently go dead, I'm actually thinking the bellhouse bushing, since it would cause the greater lateral movement. But either way it's time for some new ones. I think I'm gonna look to have a new set machined.
I'd post a picture but there's nothing to see, just some flakes of bronze.
But hey, I got nearly three years to the day out of them! pretty stoked about that. I honestly didn't think it'd last more than a year.