Well since I've been home I've been driving around a lot. There were two immediate things I noticed needed to be taken care of; the speedometer screamed like a banshee, and I left puddles of smelly gear oil from the transaxle every time I parked. I took care of the axle boots first, thinking they were the problem. This picture and brief description is an insult to the four hours I spent cleaning grime and stinky gear oil from the transaxle, axles and cradle horns to prep for the new boots. But there it is, one of the new boots, in all it's glory. Too bad the old boots weren't torn and the leak is coming from the axle plate.
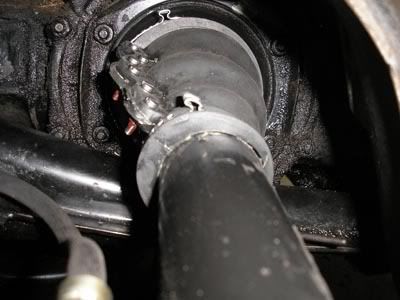
I was really amazed that the old axles weren't torn because they were the original axle boots and 40+ years old.
The speedometer was much more fun. To take it apart the glass cover needed to be pried off. then two screws from the back to take it out of it's case, and this is what's left
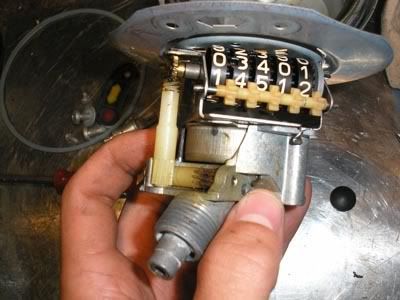
From there it split in two parts. Here is the side with the magnet; it was what made all the noise. All I needed to to was disassemble, clean and re-lube and I would have been in business, but I wanted to fart around with the odometer.
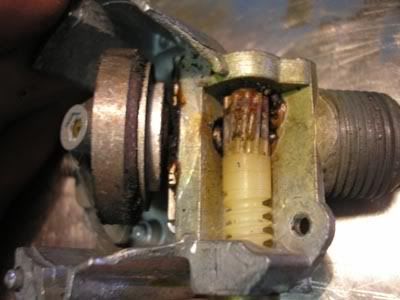
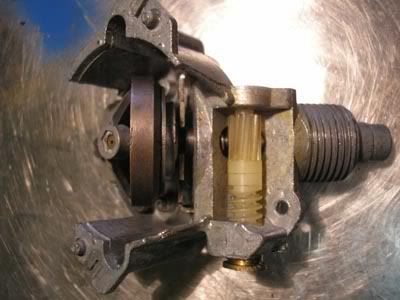
Here is the other half with the odometer and gears.
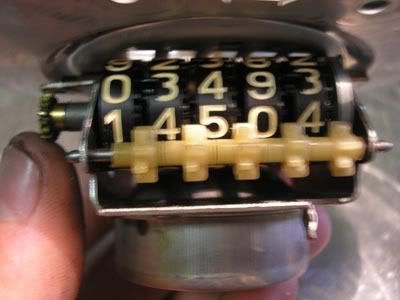
The magnet spins inside this wheel that directly turns the needle and a spring on the other side offers resistance to take the needle back to zero.
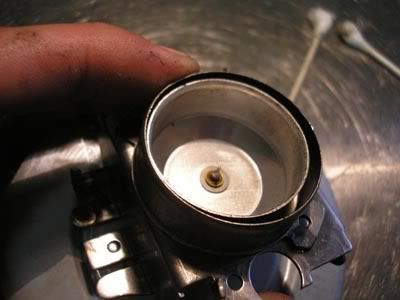
I cleaned these too and re-lubed them and then figured out how to reset the odometer. I put it at 300 miles since that is how many I figure I have on the engine.
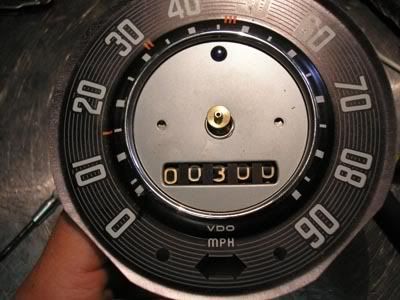
But I'm an idiot brutte and broke the needle. I wasn't going to throw away a good speedometer for a broken needle so I set out to make one.
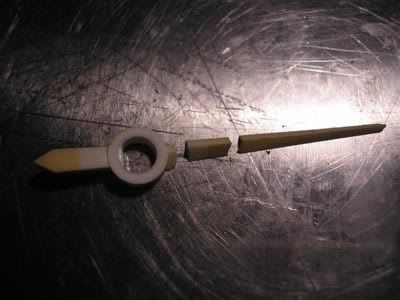
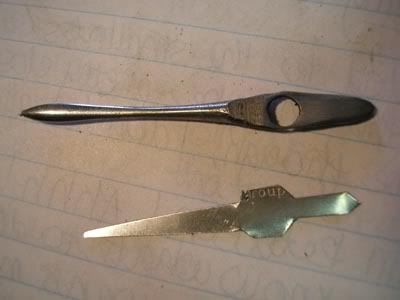
I made the bottom one first from really thin sheet metal and the top one was made out of a dentists tool. At first I didn't think about counter balancing it, but when I tested the speedometer it would barely move. I had to grind as much of the underside to make it as thin as possible and on the opposite side I soldered on a large lump to balance it out. The original needle is plastic and smaller and a LOT lighter, but I balanced it out as well as I could and put it in the car.
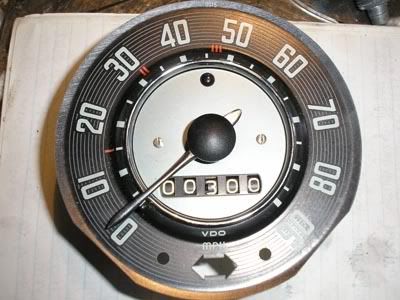
It's a little off though, especially in the higher range, but it sure looks pretty. The obnoxious whine is also gone.